
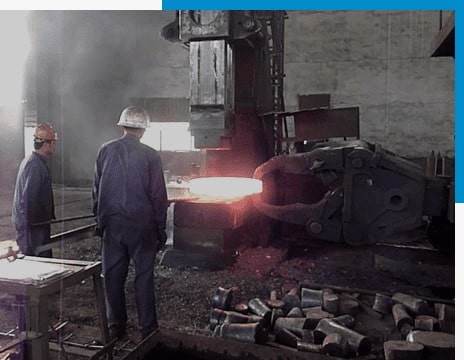
However, the inability to identify the specific area that was leaking, concerns about thermal transfer, and the thermal shock inherent in the process suggested that coating adhesion problems could further contaminate products while not fully stopping the leaks.

The company also considered coating alternatives. Metal stitching, another repair operation used on large castings with cracks, presented similar difficulties. Further, weld repair is known to cause porosity leakage along the weld transition zone, a problem similar to that the company already was encountering. In addition, welding might cause further problems with the smooth surface of the dryer. For example, in exploring the alternatives familiar to them, the company considered welding, but concluded that welding was too localized a solution. Often, various solutions are considered for such problems. Their analysis indicated that the leaking was from several small areas where the casting’s design caused porosity and some very small micro fissures around welded joints. company personnel didn’t know where the leak was or if there were multiple leaks. Leaks following porosity pathways from surface to surface prevent the casting from retaining the fluid or gas. In other applications, where the castings must contain liquids or gases, porosity prevents the casting from doing its job.

For the most part, porosity has no practical effect on casting strength and integrity, and since the majority of large castings are used in structural applications, porosity usually does not present a problem. Such challenges are typical and generally occur in large castings, as in the case of the N.J. It is the nature of the casting process, which depends on solidification of metal into a final shape, for molten material to shrink slightly, creating fissures, voids, and porosity. In these castings, as well as in smaller diecast parts, unavoidable porosity can cause leaks and make the casting unusable for its intended purpose. They are expensive and complex, they have critical dimensions and tolerances, and replacements require long lead times. Often, these castings are very large, weighing several thousand pounds. In addition, impregnation avoids the longer and often devastatingly costly process line downtime that a company encounters when a piece of key equipment goes down.įor large machines, castings play an important role as bases holding lubricants, as pumps holding liquids, and as compressor bodies holding gases. In this, and many similar cases, a large-casting impregnation process can fix potentially disastrous problems in hours or days, rather than the time it takes to replace or reface a mold or other large casting. The company could not afford lengthy downtime, and replacement of the dryer with a new one would have been costly and taken several months.įortunately, an effective impregnation process for large castings was available to fix the multiple small leaks that were causing such a big problem. Steam penetrating the wall of the casting contaminated the company’s product, causing severe quality problems that made the product unusable. diameter rotary steam dryer, a mainstay of its production process, was leaking. The casting in a New Jersey company’s 8 ft.
